The conventional ways of diagnosing and treating a medical condition are rapidly changing due to the development of novel medical devices which are being introduced in the market at a faster rate. These medical instruments are also responsible for the progress being made in the field of surgery and medicine. But medical device manufacturing is not as easy as it may seem.
Have you ever wondered how is a new medical device manufactured? What are the things to be kept in mind while designing a novel medical instrument? In this article, let us go behind the scenes of the process of medical device manufacturing and understand the science which often goes unnoticed.
The iterative process of medical device manufacturing is divided into the following stages:
- Conceptualization
- Research and development
- Prototyping
- Testing
- Risk assessment
- Risk management
- Finalizing and scaling up
Let us discuss all of the above-mentioned steps in detail:
Conceptualization
At this stage of conceptualization and ideation, the initial design of the device is conceived. First and foremost, it is essential to have a clear idea about the medical device to be designed based on its intended use. This approach clarifies the needs regarding the new medical device which it must fulfill.
Simply, the engineers have to interact with the scientists as well as healthcare professionals during this process. The healthcare personnel indicates the future use of the device which is taken as a basis as a design is constructed around it.
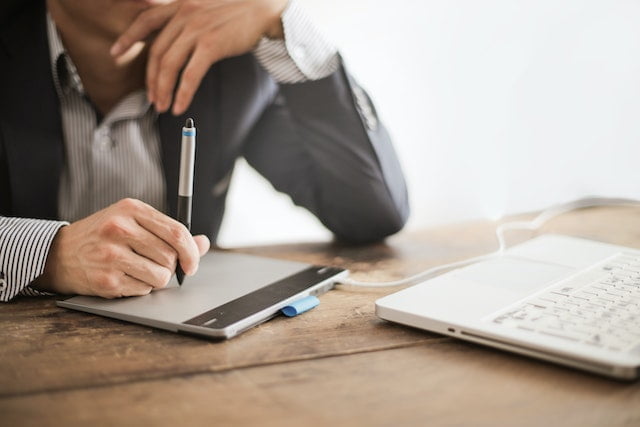
Conceptualization and ideation of a newer medical device
Research and development
The next step is to go into research and development (R&D). In this stage, the brainchild of the collaboration between different professionals is further analyzed for its feasibility. The important questions to be asked include, ‘Is the possible to manufacture a stable medical device that performs its job at least until its cost is justified?’ and ‘Does the design reflect the capability of the instrument to work in the dynamic conditions of the healthcare setups?’. Once these answers are satisfactorily answered, an initial design of the instrument along with its enlisted specifications is ready to go into manufacturing.
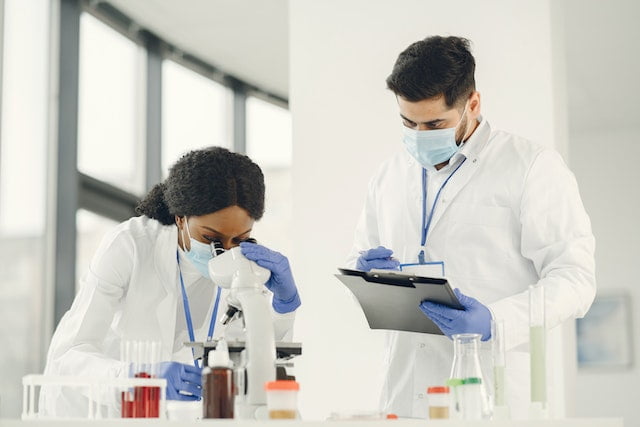
Scientists working in the research and development
Prototyping
In prototyping, the design of the medical device is put to manufacturing. At this step, the manufacturers are met with new challenges which are resolved. After multiple iterations, a prototype of the most suitably designed medical device is finally manufactured.
Testing
Once a prototype is ready, it is put to work to check its performance efficiency. This is done by installing the medical device into a healthcare setup where it is used based on the need. This way, the prototype can be tested by the consumers for whom the product is being designed i.e. the healthcare staff. Any problems which appear at this stage are reported back to the manufacturers who may alter the design accordingly.
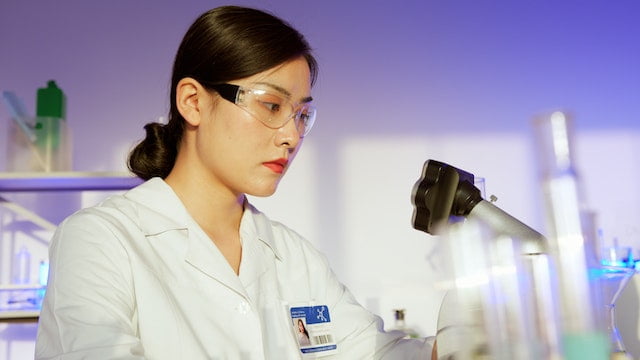
Testing of newer medical devices during development
Risk assessment as well as management
Another essential step in the manufacturing of medical devices is design control. The purpose of this step is to eliminate the risks associated with the medical device while it is in use. Just like every patient is different, every device is too. Therefore, its variables may keep on altering. Moreover, the medical device has to be adjusted according to every patient depending upon what purpose it has to serve.
These regularly occurring modifications can lead to certain risks which involve equipment malfunction as well as the need for frequent replacements of its parts. These risks, however, also vary based on the type of medical device i.e. surgical devices do not need multiple trial runs before finalizing their designs because they are relatively simpler devices.
On the other hand, the newer tools which include diagnostic and surgical robotics, artificial organs or implants, as well as prosthetics require extensive testing and design iteration prior to finalization. Therefore, based on the type of medical device as well as the extent of its use, an instrument should be evaluated for its possible risks and malfunctioning followed by their fixing.
Finalizing the design and scale-ups
Once all of the above-mentioned steps have been completed, the manufacturer has a finalized medical device that has been through extensive testing. Now, the need is only to scale up the manufacturing process to prepare multiple devices of the same design which can then be marketed.
Conclusion
The process of equipment manufacturing, just like any other item, is extensive and laborious. The team of healthcare professionals, scientists, and engineers has to work together to generate an initial design which is then prototyped and tested.
After installation of this prototype in the healthcare setup, it is employed on a daily basis for the job it is intended to perform and evaluated for its efficiency.
After further adjustments, if needed, the medical device is finalized. Thus, the process of manufacturing medical devices is, indeed, time-consuming and needs a lot of work and effort but indeed rewarding at the end of the day.
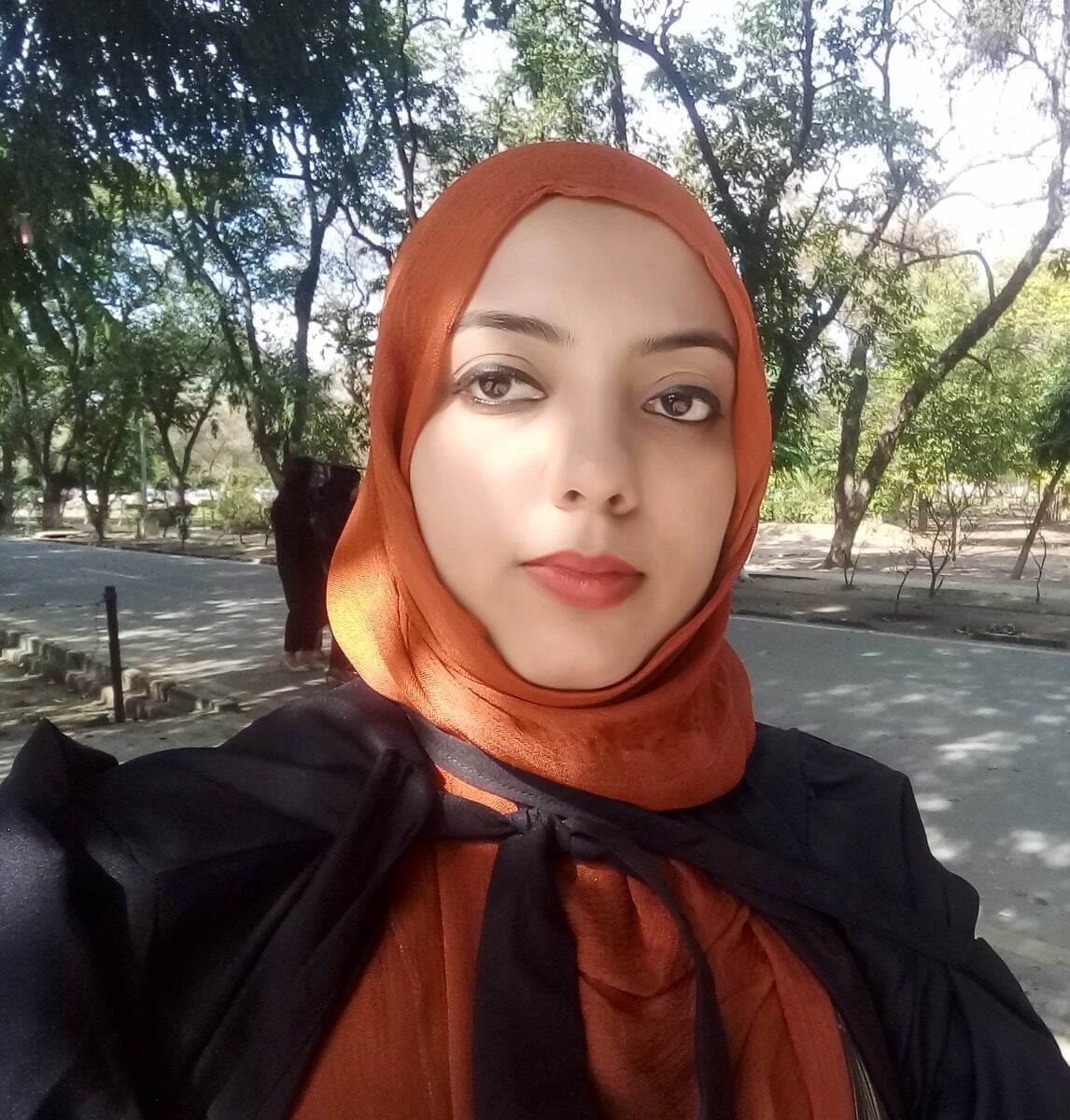
PhD Scholar (Pharmaceutics), MPhil (Pharmaceutics), Pharm D, B. Sc.
Uzma Zafar is a dedicated and highly motivated pharmaceutical professional currently pursuing her PhD in Pharmaceutics at the Punjab University College of Pharmacy, University of the Punjab. With a comprehensive academic and research background, Uzma has consistently excelled in her studies, securing first division throughout her educational journey.
Uzma’s passion for the pharmaceutical field is evident from her active engagement during her Doctor of Pharmacy (Pharm.D) program, where she not only mastered industrial techniques and clinical case studies but also delved into marketing strategies and management skills.
Throughout her career, Uzma has actively contributed to the pharmaceutical sciences, with specific research on suspension formulation and Hepatitis C risk factors and side effects. Additionally, Uzma has lent her expertise to review and fact-check articles for the Health Supply 770 blog, ensuring the accuracy and reliability of the information presented.
As she continues her PhD, expected to complete in 2025, Uzma is eager to contribute further to the field by combining her deep knowledge of pharmaceutics with real-world applications to meet global professional standards and challenges.